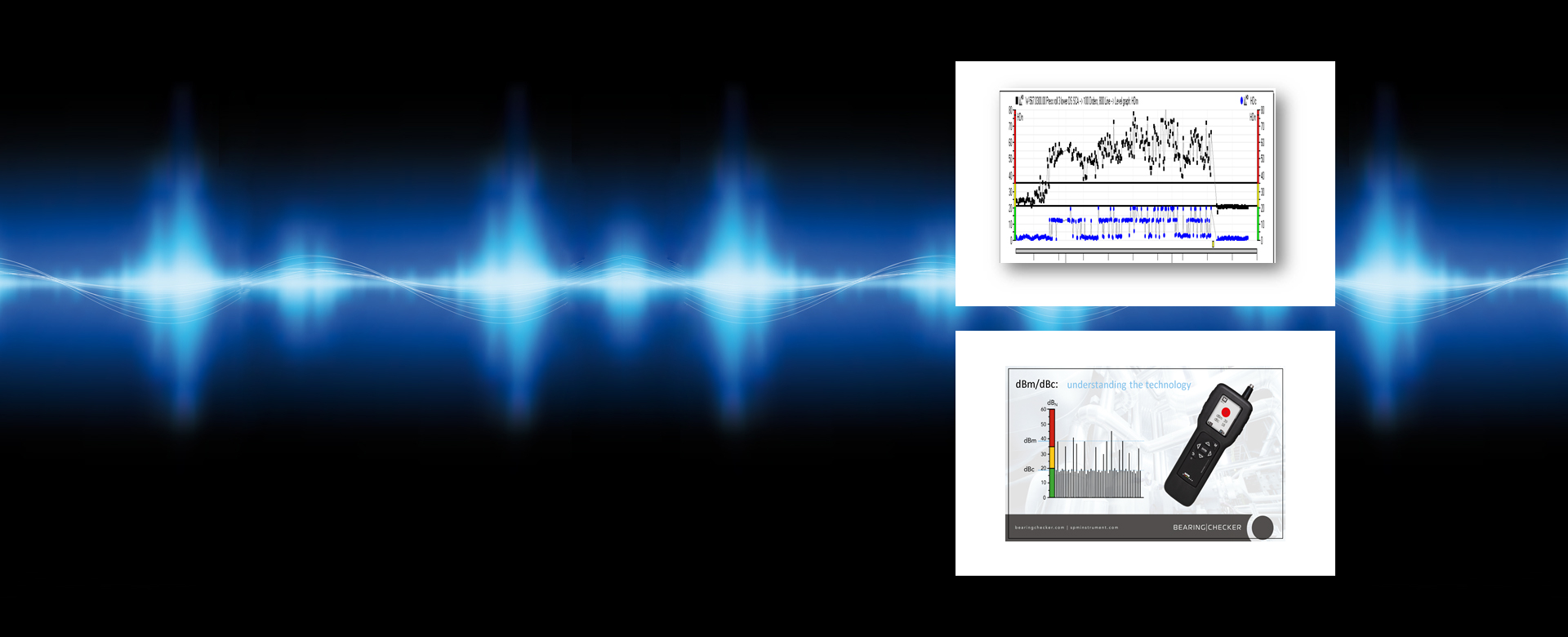
Maintenance Systems for Rotating Machinery
Basic Over-all Vibration
Measuring vibration on machinery is a measure of all the forces created during the rotor rotation. Forces such as unbalance, shaft misalignment, electrical forces, blade passing, failing bearings etc. These forces all have their own characteristics which add and subtract with one another to give an over-all vibration which is exactly what you would feel if you put your hand on the machine.
Using this over-all vibration, say velocity (mm/sec RMS) and comparing the value to standards such as ISO 10816 the health of the machine can be determined.
The SPM Shock Pulse measurement is very specific to ball or roller bearings
Click to Review Instruments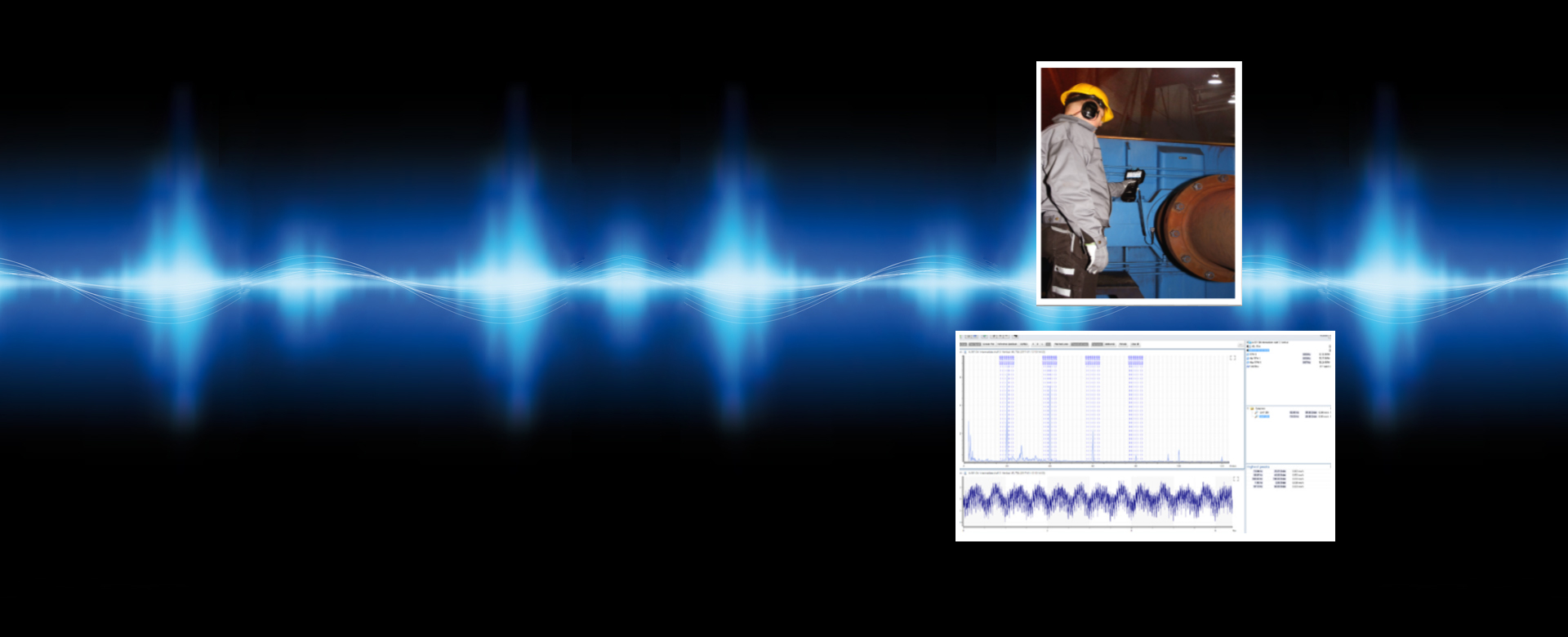
Maintenance Systems for Rotating Machinery
Vibration Analysis
Most forces are related to the running speed and are measured as the frequency (Hz or CPM) of the vibration.
Each mechanical force can have a different frequency such as unbalance only occurs at 1x RPM where as a blade passing frequency of a fan or the mesh-frequency of a gear will generate a frequency equal to the RPM X Number of fan blades or gear teeth.
Some mechanical forces are not related to the rotational RPM such as ball or roller bearings generate shock forces which are resonances of the bearing race way elements.
To separate vibration frequencies we use a mathematical algorithm FFT Analysis (Fast Fourier Transform) to calculate each frequency in the vibration signal.
Click to Review Instruments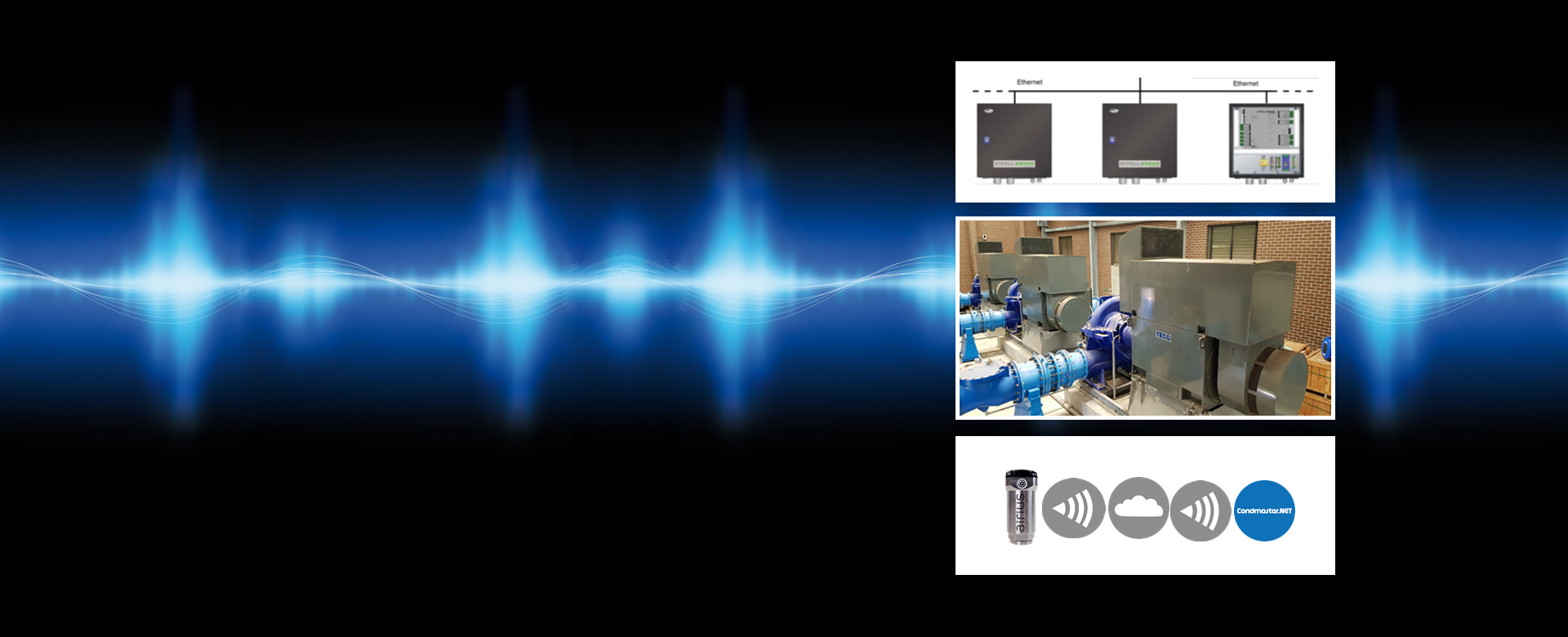
Maintenance Systems for Rotating Machinery
On-Line Condition Monitoring
On-Line vibration condition assessment for critical plant is now more widely used as it offers continuous protection to avoid unplanned issues such as a bearing running dry, resulting in a collapsed bearing and catastrophic failure. On-Line monitoring systems can be interfaced to PLC/SCADA control systems to give full machine protection.
The latest innovation is to use Wi-Fi wireless X,Y,Z transducers which simplifies the installation costs and can relay condition data via modems to stand-alone software or Cloud based software.
Click to Review Instruments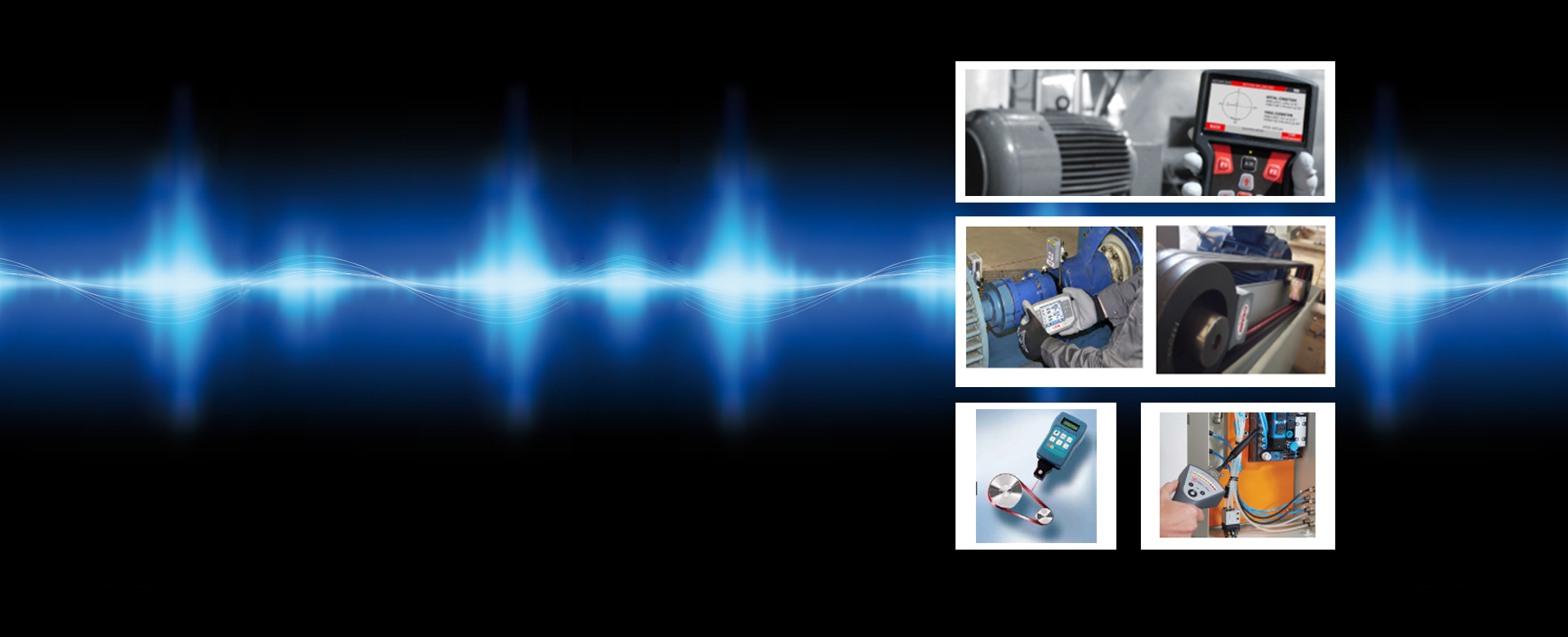
Maintenance Systems for Rotating Machinery
Correction Tools
Once excessive vibration is detected either field repair or workshop refurbishment is necessary.
Using portable instruments field dynamic balancing of fans may be practical but access to the rotor must be possible to add or remove weight.
Shaft & pulley alignment are another very common cause of unwanted vibration and using portable laser alignment instruments can give excellent accurate results.
When aligning pulleys it is also important to ensure that the belt tension is correct by using a laser belt tensioning tool,
Click to Review Instruments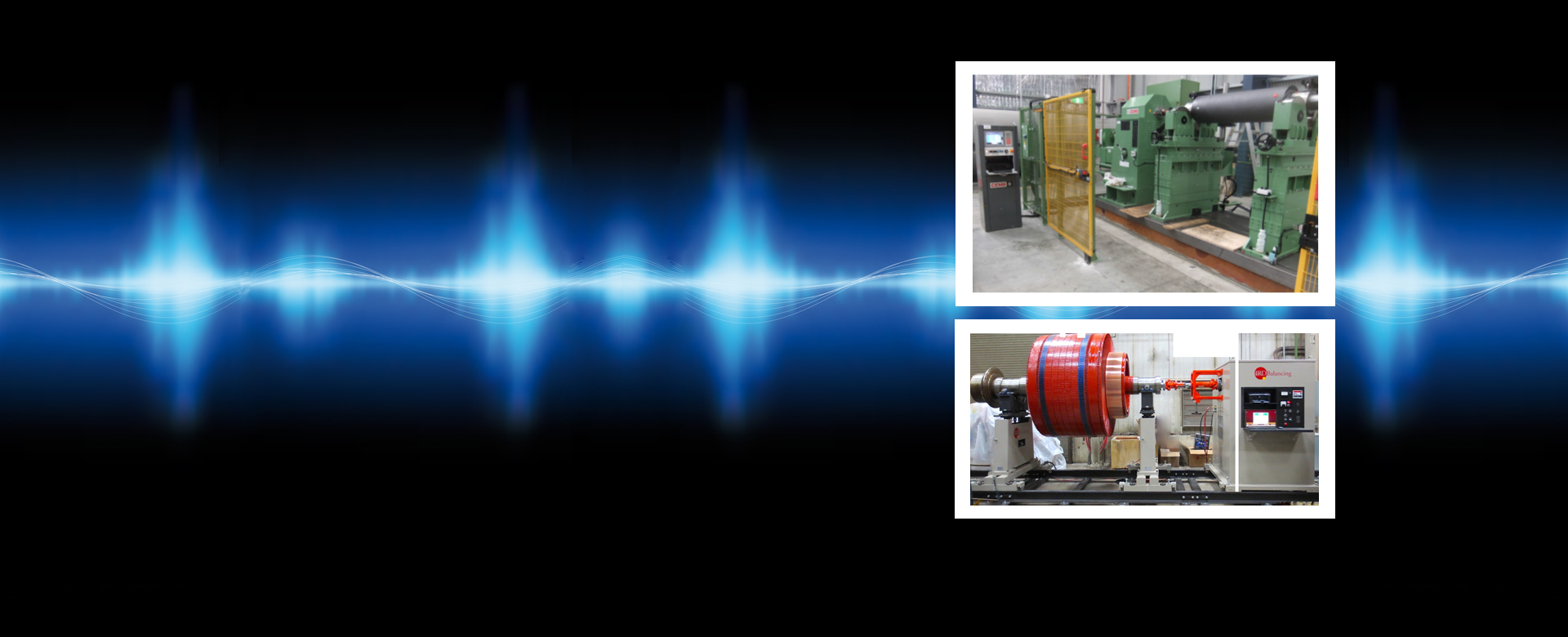
Maintenance Systems for Rotating Machinery
Workshop Dynamic Balancing
The final activity for new or repaired machines is that they must be dynamically balanced in a workshop balancing machine.
As the final vibration due to unbalance is proportional to the residual unbalance and the force, due to unbalance, is proportional to the square of the rotor speed it is important to achieve a low residual balanced condition.
Some of the benefits of having low unbalance forces are, increased life from roller or ball bearings, better bearing lubrication in bearings, reduced running temperatures and better finished quality when milling grinding or drilling.
Click to Review Instruments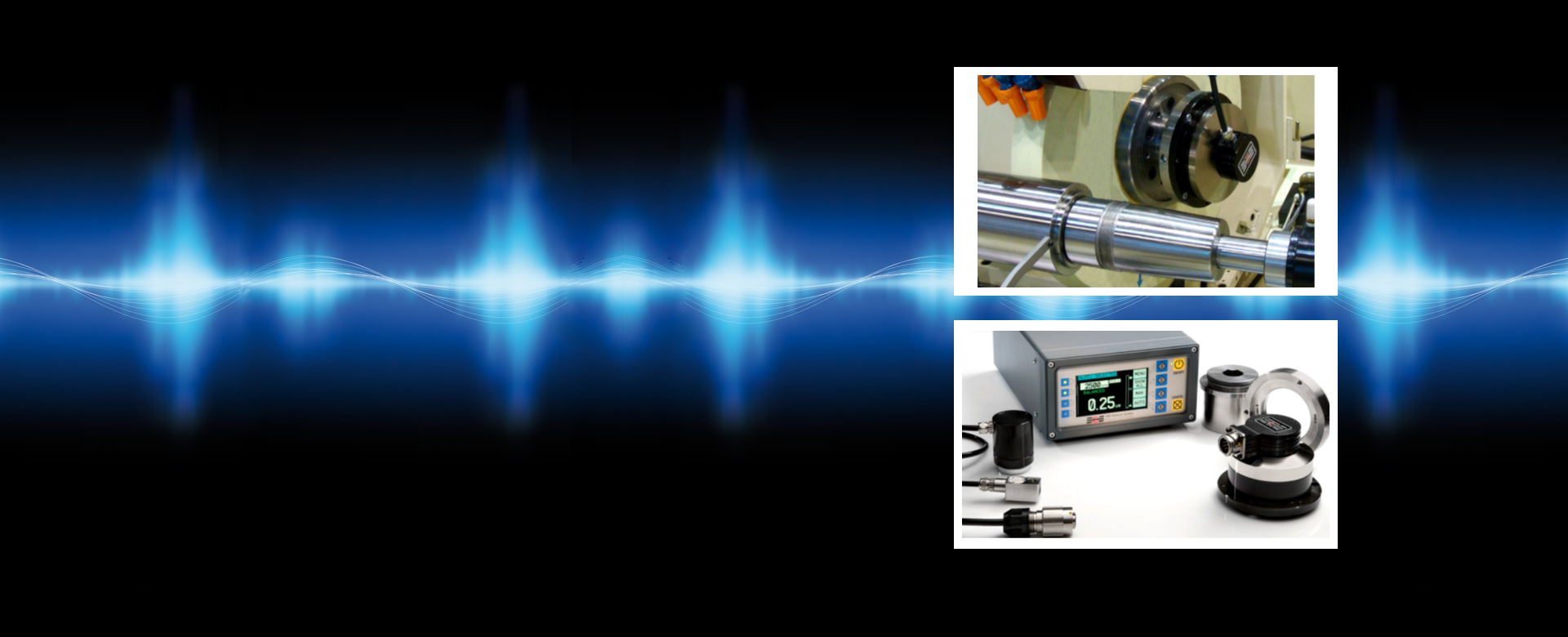
Maintenance Systems for Rotating Machinery
Continuous Production Dynamic Balancing
For high speed grinding the unbalance created as the grinding wheel wears away decreases the final finish on the part being ground. This can mean that a second pass must be made to achieve the desired finish quality.
With automatic continuous balancing of the wheel as it is used results in a constant quality finish thus eliminating multiple grinding passes, reduced grinding time, increased machine bearing life due to lower unbalance forces.
With high speed spindles, cutting tools and milling bits well balanced product quality is assured.
Click to Review Instruments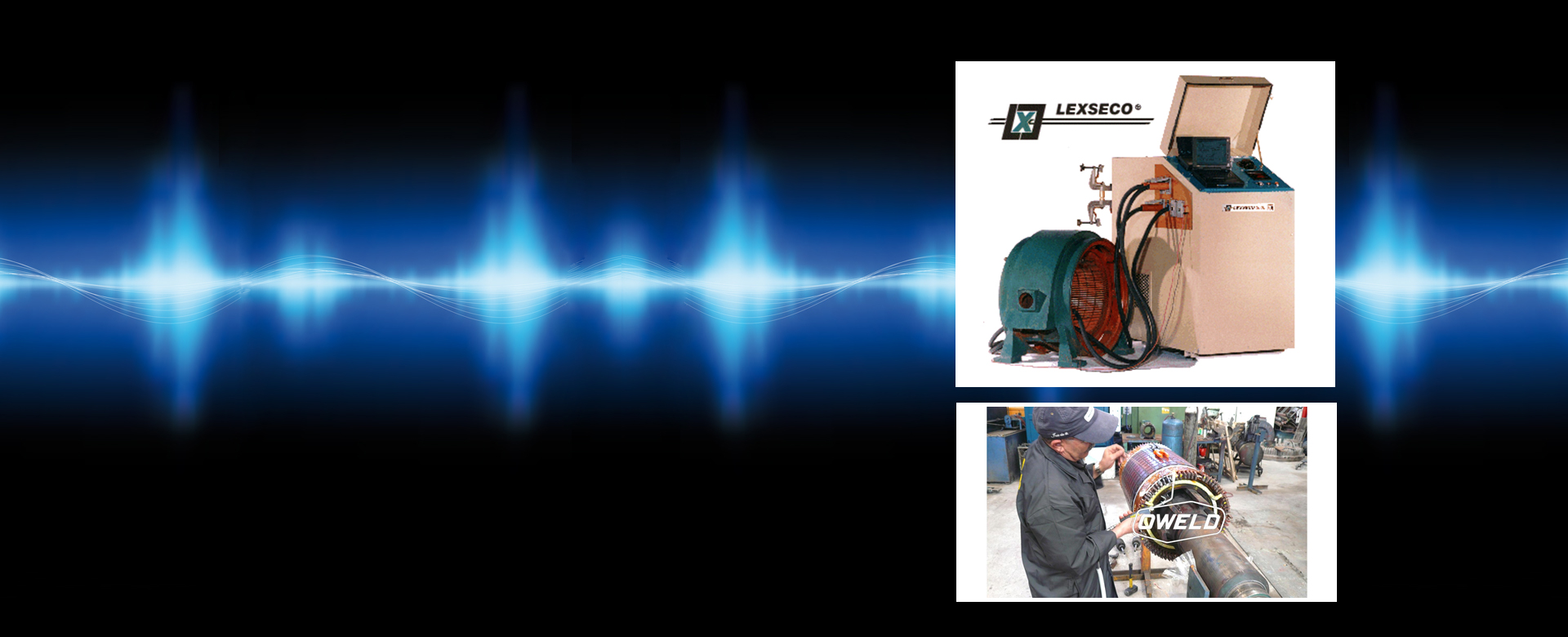
Maintenance Systems for Rotating Machinery
Electric Motor Repair
At the commencement of motor repair it is critical to ensure that the integrity of the motor core meets acceptable standards. Lexseco have developed the MP7 Software which is used with their range of Core loss Testers to generate “Multiparameter” tests to simplify core and hotspot testing on stators rotors and armature cores.
Another important electric motor repair activity is terminal brazing which has traditionally been done using a gas mixture of acetylene ond oxygen supplied in gas bottles.
Oxyweld have revolutionised the brazing process by the electrolysis of water to produce hydrogen and oxygen which when mixed and ignited produces a flame of 3,650ºC
Click to Review Instruments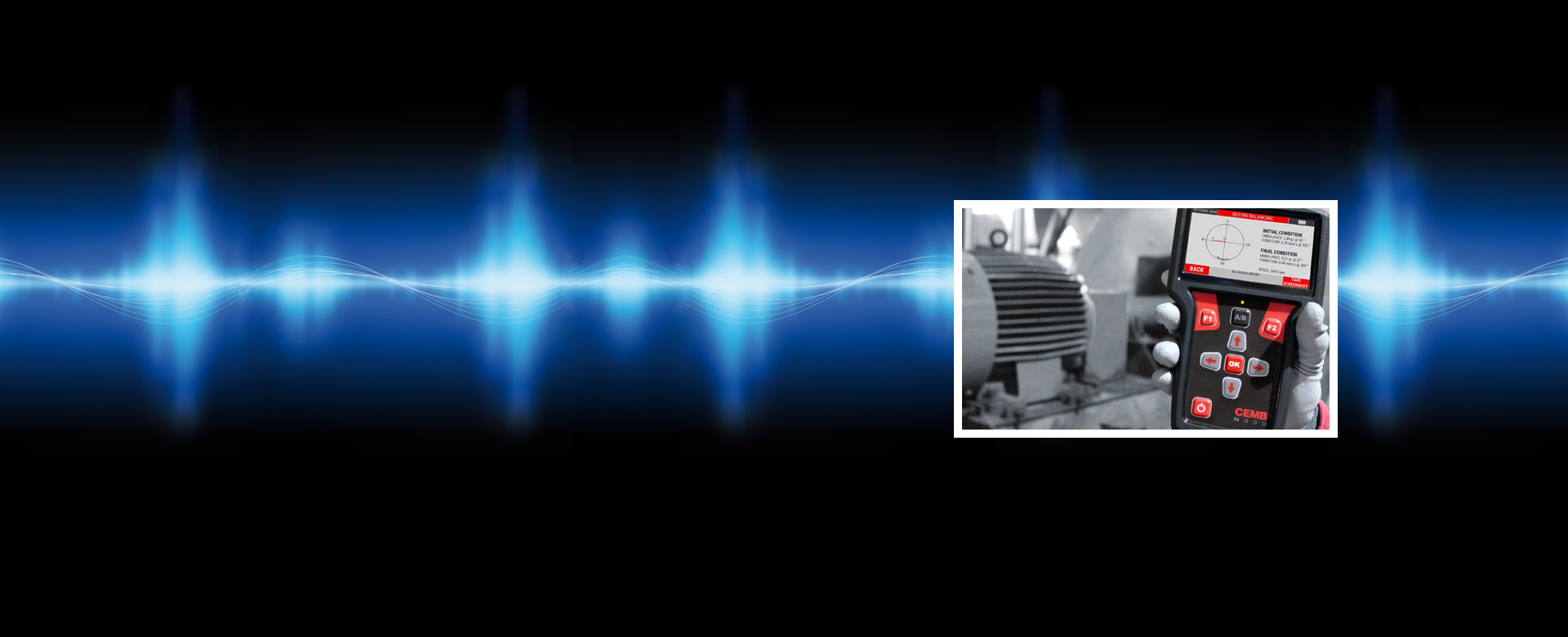
Maintenance Systems for Rotating Machinery
Supporting Services
- Instrument Repair service.
- Calibration Service Traceable to NMI & Aust. Standards.
- In house precision dynamic balancing of rotors up to 4 Kg capacity
- On-site Commissioning Service & Installation Supervision.
- On-site Customer Training in Vibration Techniques , Dynamic Balancing and Laser Alignment of shafts and Pulleys.
- On-site Vibration Measurement & Analysis trouble shooting.